As manufacturing automation rapidly advances, conveyors are not only being used for transportation but also accurate material (or product) placement. They are often required to deliver product to a precise location consistently. When transporting product by conveyor, equipment choice will greatly impact the system’s ability to reliably deliver to a target position — either stationary (indexing) or dynamic in nature. This article explores some common conveyor types and compares the ranges of positional accuracy you might expect with each type.
Below, we will use results published by Dorner Manufacturing in 2019 for comparisons between crowned pulley and knurled v-guided conveyor performance, plus published data from various conveyor manufacturers. Multiple factors can impact the final product position. However, for this discussion, it is assumed that the material can be placed accurately and travel without slippage on the belt surface, and with no additional fixturing used. Pulley Lagging Types
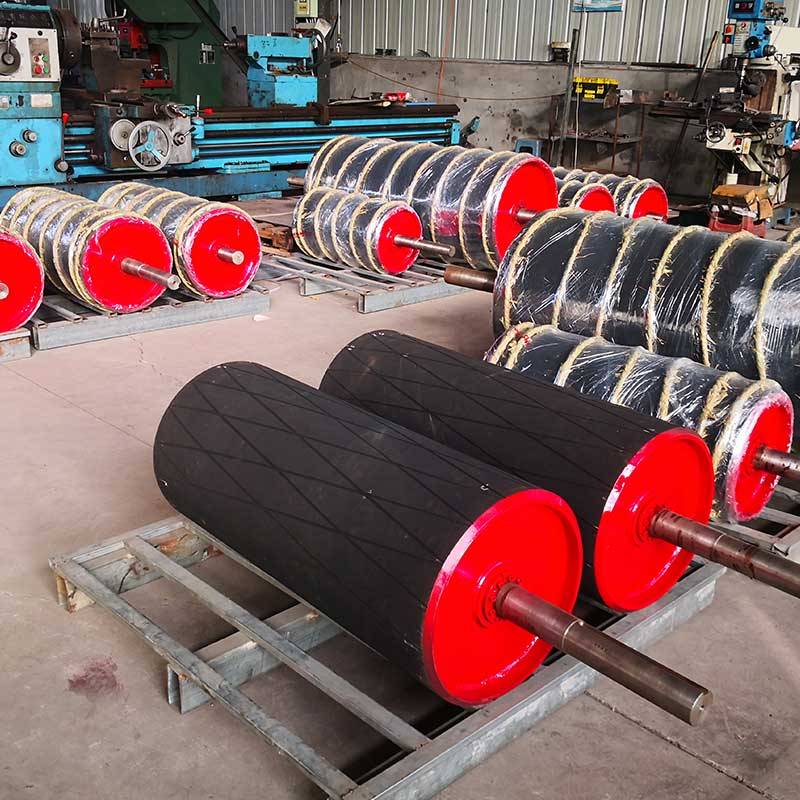
Historically, conveyors have simply provided a method of transporting products from one location to another. Using conveyors in manufacturing is widely accepted as essential, as they provide many easily recognized benefits. While understood to be critical, they are often an afterthought in the system design process.
One of the most recognized benefits is the reduction of labor involved in transporting product between manufacturing processes. Another key benefit is reduction of work in process (WIP), which can result in lowered material-carrying costs, or in some cases, loss due to scrap (scrap can occur when material is placed in containers or handled during transportation). Alternately, in some applications, conveyors can be used to intentionally increase material as a buffer between processes to improve overall equipment effectiveness (OEE). Safety can be a crucial driver to using conveyors as they remove workers from direct contact with machinery and can potentially eliminate some repetitive motion injuries.
For this article, it is important to clarify some vocabulary. Belt tracking, as used here, refers to the side-to-side (x-axis) movement that occurs as a belted conveyor runs. This movement is based on the belt surface position relative to the drive and idler spindle centerline. While similar sounding, conveyor tracking (y-axis) is used in robot applications where the moving conveyor’s speed is calculated so that a robot can pick or place moving objects on the dynamic surface. The term drift refers to the discrepancy between the rotational distance traveled by the drive spindle circumference and the actual distance the belt has traveled. This variance is anticipated, and the actual position is caused by a micro-slippage of the belt on the drive spindle.
Crowned spindle conveyors have been used to move coal and ore since their invention in 1892 by Thomas Robins. In 1913, Henry Ford introduced the conveyor belt on his assembly line at Ford Motor Company. At that time, conveyors relied primarily on crowned spindle design. The crown refers to a spindle with a slightly larger diameter at the drive surface center than at the edges. The physical phenomenon of conveyor belts following the largest diameter of the spindle and thus being self-centering or tracking is fascinating. This method of conveyor tracking has been accepted for over a century.
When pushed to one side, the belt will automatically find its way back to the spindle’s center. The fact that the belt self-centers after disruption acknowledges that it can also wander to some degree or be pushed laterally out of place. This can happen for various reasons, such as belt inconsistencies, uneven loading on the belt, or transferring material on or off a conveyor with lateral forces, such as a side transfer of products. It is worth noting that when running in the non-preferred direction, the crowned pulley’s ability to track accurately is rather poor. The preferred direction is with the driven spindle pulley at the discharge end.
Results will vary depending on the conveyor’s configured length, width, and speed. One such test was recently run, and the results are below.
Some manufacturers add a v-guide strip to the back of the conveyor belt to allow for more accurate belt tracking. By applying such a belt to a conveyor with v-guide grooves in the drive, idler pulleys and the conveyor bedplate, the belt will be less likely to track or wander from side to side. This manufacturing process adds cost but has several advantages, including easier setup. The knurling or raised diamond pattern machined into the spindles can also reduce belt drift. However, this pattern is less practical when applied to a crowned pulley. The results for both tracking and drift can be significant. Notice that lateral and axial movement have decreased.
Precision conveyors are a somewhat new category of belted conveyors that can match the tracking characteristics of a v-guide belt while eliminating drift. This conveyor type can be either flat belt or fixtured. While more precise methods of product placement are mentioned later in this article, this conveyor style can be a lower-cost alternative. Adding a servo motor to a precision-belted conveyor can enhance its performance capabilities, such as higher speeds, higher accelerations, and more precise indexing to position. Notice that there is now no drift.
Pallet conveyors come in various styles that use lift-and-locate modules for pallet positioning. While more expensive, pallet conveyors offer several benefits, including precise product placement. The tradeoff is that the pallet needs to stop and be lifted into location using pins that align into the pallet’s base. Pallet conveyor accuracy is not impacted by either drift or wandering, since the pallet comes to a stop for accurate positioning.
Accuracy numbers presented will vary and are intended to illustrate general guidelines. Always consult your conveyor manufacturer for their published data and general guidance.
These conveyors are distinct in two ways. First, the product being transported is not riding on a flexible belt directly; it is generally nested in a fixture attached to the pallet, which acts as a carrier. The fixture helps ensure that the product alignment is consistent throughout the process. The second difference is that they are asynchronous — the individual pallets are held in place long enough to complete the process. The pallets can be released into a zone to stay in queue or proceed directly to the next lift-and-locate station.
The various styles of pallet conveyors include flexible chain, open-center dual strands, and open-center edge rollers. Each uses unique yet similar lift-and-locate devices to accurately position the pallet once it arrives at the lift-and-locate station. Notice now that both lateral movement and axial movement are very small.
By understanding the positional accuracy characteristics of various conveyors (Table 1), you can select and apply an appropriate product to meet or exceed your application needs. While it may be tempting to choose the least expensive product to move and position products, it is important to remember the impact that this can have on the OEE of your equipment. An inability of the installed product to meet your positional accuracy requirements may significantly affect your production capabilities in terms of quality and throughput.
Recently, we have seen the trending application of timing belt style conveyors, both flat belt and fixtured types. Precision belted conveyors with servo control, high speed and throughput capabilities, and eliminated belt drift are particularly useful in robotic applications. Precision timing belt conveyors are increasingly popular, where a mixture of high accuracy and throughput is critical. There will always be a need for pallet-style conveyors, as high-precision assembly work often requires more accuracy than any current belted style can offer.
This article was written by Dan Toynton, Conveyor Specialist, Motion Ai (Birmingham, AL). For more information, visit here .
This article first appeared in the April, 2023 issue of Motion Design Magazine.
Read more articles from this issue here.
Read more articles from the archives here.
EV Battery Recycling Still Being Defined
4D Printing with Smart Materials
Leaders Optimistic North America Lithium Supply Gap Can be Eliminated
Zinc-Air Batteries: A Cheaper, Safer Alternative to Li-ion Batteries
2023 Battery Show North America Opens as Automakers, Suppliers Intensify...
How Much Do You Know About Drones?
Software Solutions for Battery Management System Applications With AUTOSAR
Leveraging Electronics Digital Twins on AWS to Accelerate Software-Defined Vehicle Validation
Choosing a Silicone for Operation in Harsh Thermal Environments
Scan-Based and Project Design for Medical
Introduction to the Integration of Electronics Switching and Modules in Commercial Vehicles
By submitting your personal information, you agree that SAE Media Group and carefully selected industry sponsors of this content may contact you and that you have read and agree to the Privacy Policy.
You may reach us at privacy@saemediagroup.com.
You may unsubscribe at any time.
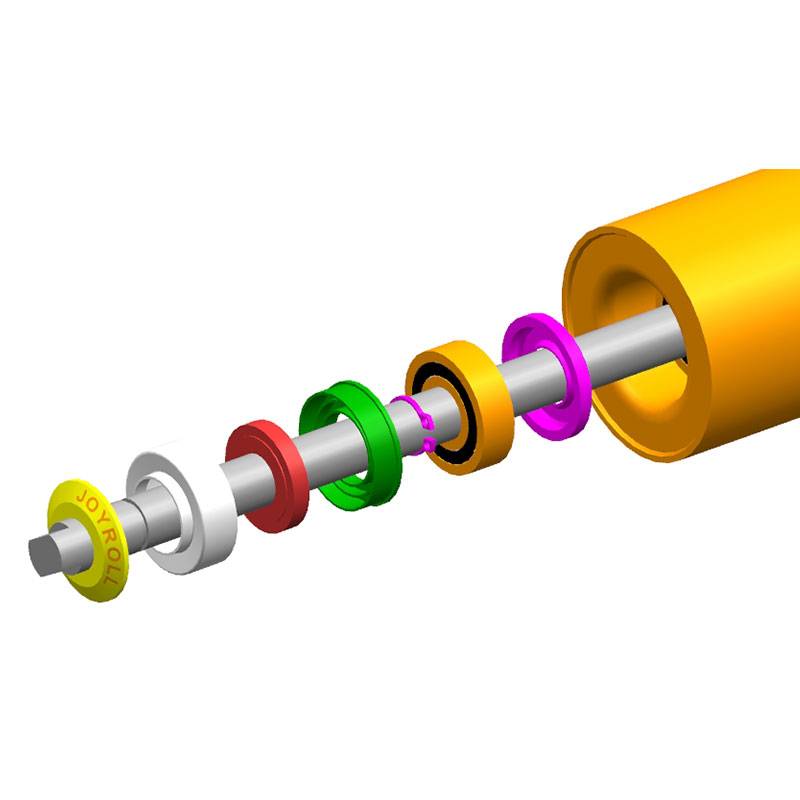
Conveyor Rollers Suppliers © 2009-2023 SAE Media Group