The cement and steel industries are notoriously hard to decarbonise, yet their production plants are generating the solution: waste heat. Tobias Panse of Siemens Energy explains.
Few industrial processes generate as much CO2 as cement production. Crusher Companies

It takes limestone and crushes, burns and grounds it using a huge amount of energy until it becomes the powder that is the world’s most ubiquitous building material. At the core of this process sits the preheater and the rotary kiln, processing ground limestone and clay at temperatures of more than 1,300°C.
That’s a lot of heat… yet in many cement plants, much of it still disappears via flue gases and surface dissipation – as much as 40%-45% of what’s put in. This is where waste heat recovery (WHR) comes in. The waste heat of the kiln and other areas of the plant can be reused, providing up to a third of the plant’s power requirements.
In industry, there are many applications for waste heat recovery, including power or process steam generation, space heating and cooling or district heating. Yet, it arguably has its biggest potential in hard-to-abate industries like cement, steel or petrochemicals.
But still, many cement plants around the world don’t utilise this energy-efficient way to cut their emissions, despite their need to decarbonise while maintaining energy efficiency and profitability.
This article is part of the ‘Future Energy Perspectives’ series, in which experts from Siemens Energy share their insights into how we can move towards a decarbonised energy system.
The cement industry has its work cut out: it is the third-largest industrial energy consumer and accounts for around 7% of industrial CO2 emissions globally.
While it is making progress in reducing its carbon footprint, more aggressive action will be required to meet intermediate emissions targets and drive a successful energy transition. And while WHR is not the only tool to reduce CO2-emissions in the cement industry – carbon capture is another option – it is one of the measures that pays off most quickly.
In 2021, the Global Cement and Concrete Association (GCCA) published a formal roadmap for achieving net zero carbon emissions by 2050.
The roadmap establishes an intermediate target of cutting greenhouse gas emissions by 25% by 2030 – which will require aggressive action from producers in the next two-to-three years.
By and large the best place to capture waste heat in a cement plant are flue and waste gas streams from the pre-heater tower and the clinker cooler. However, there is no one size fits all solution: for every cement plant – just like in other hard-to-abate industries – WHR solutions must be customised. This is because waste heat recovery depends on various factors: waste heat temperature, composition, kiln capacity and raw material moisture content.
Therefore, a detailed analysis is required before implementing any solution.
To determine the most efficient way of generating power from WHR for cement, as well as for steel and petrochemical plants, Siemens Energy has conducted several studies looking at different technical options.
They all use a similar setup: they consist of a boiler with liquid that is heated by the waste heat until it creates hot vapour, which then drives a steam turbine. Afterwards, the steam flows to a condenser to cool down before it is pumped again through the boiler.
What mostly differentiates these options is the medium used. Our tests show the traditional method of superheated steam cycle with its higher temperatures and higher power output best fit most applications in cement and even in steel plants.
Yet, the alternatives should not be dismissed. For example, more and more installations also use the Organic Rankine Cycle (ORC), using organic fluids. Its main advantage is high efficiency for lower temperatures and that it doesn’t require any water.
More Future Energy Perspectives Decarbonising heat: The hot topic we can’t ignore Replacing F-gases in switchgear: a revolution in the making How disruptive service solutions will re-energize power plants Scaling up clean fuels for net zero Kicking out coal and greening gas on the road to net zero
Another, the Supercritical Carbon Dioxide Cycle, is still at the R&D stage, but the first demonstrators are being tested. For example, funded by the EU-project CO20LHEAT, a cement manufacturing plant in Prachovice, Czech Republic, used heat at temperatures of 400°C compared with lower temperature steam and organic rankine cycle solutions.
We are currently looking for other partners to develop another pilot plant alongside.
Additional heat in cement and other plants of hard-to-abate industries can be recovered from hot exhaust streams via a heat recovery steam generator (HRSG) for sites that utilise on-site power generation with gas turbines.
As there are several different types of HRSGs (drum-type, once-through etc), working closely with original equipment manufacturers to determine the optimal configuration is critical. The design of the steam cycle and optimal sizing of the steam turbine are also important to ensure maximum power output, given the available thermal energy.
These methods can also be applied in steel production, which lags in their usage of WHR systems compared to the cement industry. There are reasons for this: heat sources in steel plants are more difficult to access, and processes, such as the Electric Arc Furnace, are discontinuous.
Yet, these challenges can be overcome. At Siemens Energy, we are working closely with steel customers to develop new customised solutions to improve steel plant operating efficiencies and to reduce their carbon footprint. The key is to incorporate the various heat sources, use heat storage where possible, and install smart control systems.
Obviously, other options to take advantage of waste heat can be integrated, creating hybrid solutions, and one is industrial heat pumps. While they have not been widely used for WHR in hard-to-abate industries yet, this will likely change as the industry seeks additional decarbonisation pathways.
A successful recent application of a large-scale heat pump by Siemens Energy is the world’s first 8MW-high-temperature heat pump, located in Berlin at Potsdamer Platz.
Using waste heat from a cooling plant, it upgrades and feeds into the city’s district heating network flexibly at temperatures between 85°C and 120°C.
Further progress has been made to extend this range up to 270°C using subsequent steam compression. Such configurations recently became bid-ready in the marketplace.
Another option to drive decarbonisation with waste heat is carbon capture.
Most carbon capture systems, including amine-based solutions, require heat/steam to release CO2 once it has been absorbed by the amine. The solvent then must be cooled for absorption so it can be regenerated and recycled.
While the low-pressure steam generated from combusting flue and waste gases can be sufficient to meet the capture system’s heat demands, it will reduce the amount of available steam for power generation.
Heat pumps can also be installed to capture the thermal energy from solvent adsorption, as well as from the CO2 compressor or the exhaust of gas turbines. Doing so improves the carbon capture system’s overall efficiency and maximises the steam turbine’s net power output.
Download your copy of ‘Harnessing waste heat to decarbonise cement and steel’
What will drive the adoption of WHR technologies? The biggest factors are power and emissions pricing, government regulation, and cost competitiveness.
A limiting factor – at least currently in cement plants – is the focus on increasing production, which leaves limited investment available for improving efficiencies.
China and India show what is possible in terms of WHR adoption through government legislation and cost competitiveness.
Finally, for any solution, co-creation is key. WHR solutions are tailored not just to a single industry, such as cement or steel plants, but also depend on local factors – such as electricity cost and availability, the other industries close by, climate conditions, and more.
Taking in these factors, we worked closely with an Indian company to co-create WHR solutions that offered the best possible performance at optimal cost.
They were tailored for each plant, fitting within the available site conditions. It showed that working together on cost-optimised WHR solutions is not only possible but achieved best by working together.
Tobias Panse is Senior Vice President of Industrial Steam Turbines and Generators at Siemens Energy.
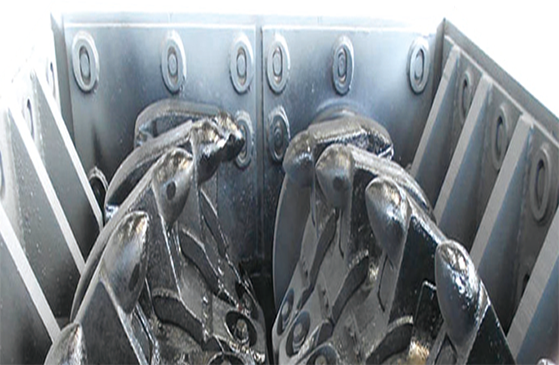
Roll Crusher For Coal Power Engineering International examines the drivers that are changing the global power generation sector. It delivers up-to-date news and in-depth articles on industry trends, new technologies and cutting-edge projects impacting the global energy transition. It is a hub for thought leadership from industry experts who are shaping the 4th Industrial Revolution.